what is cemented carbide end mill?

一、tungsten carbide end mill
Tungsten carbide end mill is tungsten carbide (WC) as the main raw material, made into carbide round rod, through the powder metallurgy process made of high-performance cutting tools. The cutter body has high hardness, high temperature resistance, and can be qualified for milling, grooving, contouring and other tasks of steel, cast iron, aluminum alloy and other materials. Compared with high-speed steel tools, cemented carbide end mills have a longer life, especially for high-precision, mass-production scenarios.
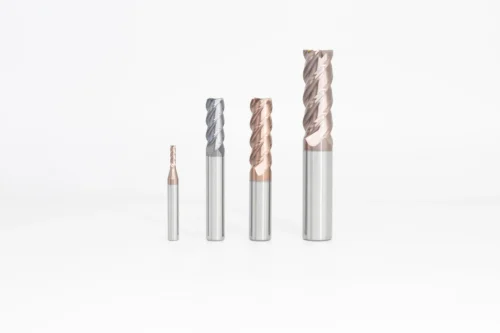
二、End mill diameter and standard dimensions:
The diameter of end mill is one of the core parameters that determine the machining efficiency and accuracy. The larger the diameter, the stronger the tool rigidity, suitable for heavy cutting; The smaller diameter is suitable for fine machining or narrow space operation.
Common end milling cutter sizes range from 1mm to 50mm, and users need to choose according to the workpiece material, machining depth and machine power.
Puwei universal end milling cutter size parameters:
In the mold processing, if you need to open a narrow slot or carve details, choose the end mill diameter of 3-6mm tool is more flexible; In the face of large workpiece surface milling, large diameter tools above 12mm can significantly improve efficiency.
According to the different needs of processing, choose different diameters of end milling cutter,
三、Standard end mill diameter:
In order to meet the general processing needs, the industry has formed a standard end mill diameter series, such as 1mm, 2mm, 3mm, 4mm, 6mm, 8mm, 10mm, 12mm, 16mm, 20mm and so on. These standardized dimensions not only facilitate the user’s quick selection, but also ensure the compatibility of the tool with the fixture and machine tool.
It is worth noting that some special scenarios (such as aerospace or medical device processing) may require custom non-standard sizes, but in most cases, following the standard end mill diameter can effectively control costs and shorten delivery times. Of course, according to the different processing needs, the choice of standard end mill diameter will be different.