Recommendations for best insert radius for finishing milling steel
When finishing steel parts, the best insert radius usually depends on the specific requirements and conditions of the operation. Generally speaking, finishing milling steel, such as 0.2mm or 0.4mm, are more suitable for finishing operations.
These smaller radii can work at shallower cutting depths, reduce vibration, and thus obtain better surface finish.

Recommended radius range:
General finishing: 0.4–1.2 mm (common range)
Small radius (0.2-0.4mm): suitable for high surface finish requirements (such as Ra 0.8 μm or less), but the tool wears faster.
Medium radius (0.8–1.2 mm): balances surface quality and tool life, suitable for most finishing scenarios.
High hardness steel (such as hardened steel): 0.2–0.5 mm is recommended to reduce cutting forces and avoid chipping.
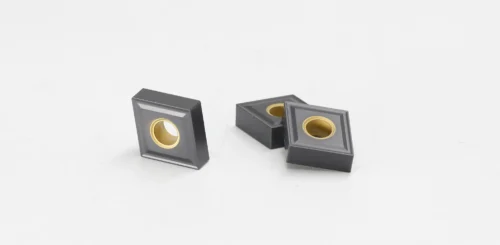
For example: a 0.2mm radius insert is suitable for light finishing operations, while a 0.4mm radius insert can work at a slightly larger cutting depth while still maintaining a good surface quality.
It should be noted that the cutting depth also needs to be considered when selecting the insert radius. The cutting depth should be greater than the insert feed rate. It is usually recommended that the cutting depth is 2-3 times the feed rate.
In addition, if the cutting depth is less than the insert radius, it may cause excessive friction between the insert and the workpiece surface, affecting the surface quality.
In short, when finishing milling steel parts, it is recommended to select a 0.2mm or 0.4mm insert radius and adjust the cutting parameters and surface quality according to the actual processing conditions.