Carbide turning tools: turning inserts for efficient metal processing
In the field of metal processing, carbide turning tools (Turning Tool) have become an indispensable cutting tool in lathe processing due to their excellent wear resistance, high hardness and long life.
Whether it is rough processing or fine processing, choosing the right turning tool (Lathe Tool) can significantly improve production efficiency and reduce costs.
We will recommend several classic carbide turning tool models for you and analyze their applicable processing materials and scenarios.
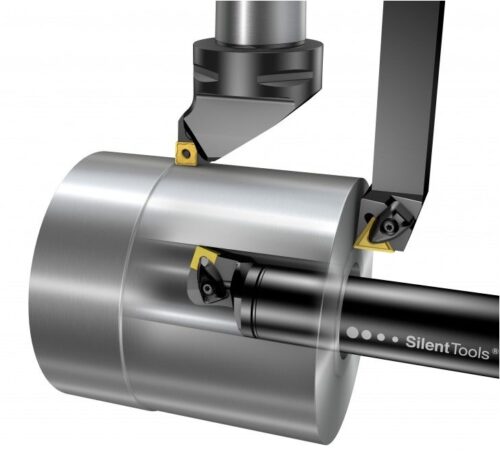
Core advantages of carbide turning tools
1. High hardness: Carbide materials (such as tungsten-cobalt) can easily handle high-hardness metals such as steel, stainless steel, and cast iron.
2. High temperature resistance: In high-speed cutting, the tip of the tool can withstand high temperatures above 800°C to avoid rapid wear.
3. Strong versatility: By changing the blade shape (such as diamond, triangle) or the edge angle, it can adapt to different processing needs.

Recommended turning tool models and application scenarios
1. Roughing turning tool (such as Puwei CNMG-PV)
Applicable materials: carbon steel, alloy steel, cast steel.
Features: large rake angle design, smooth chip removal, suitable for strong cutting.
Scenario: automotive parts blank processing, heavy machinery shaft rough turning.
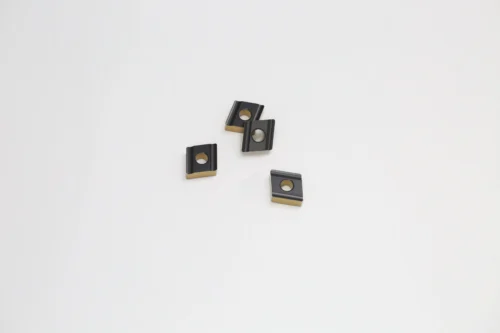
2. Finishing turning tool (such as Puwei CNMG-mA)
Applicable materials: stainless steel, high-temperature alloy (such as Inconel).
Features: sharp cutting edge and coating technology to achieve high surface finish.
Scenario: aerospace precision parts, medical device parts finishing.
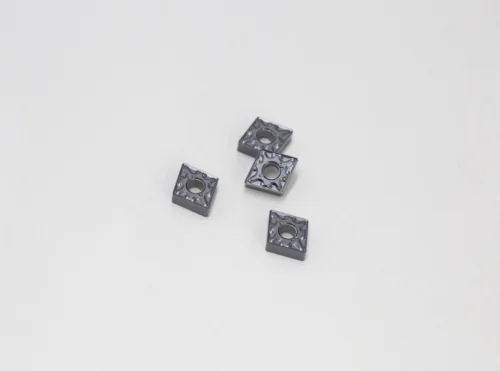
3. Multi-function turning tool (such as Puwei general turning tool CNMG-43)
Applicable materials: cast iron, non-ferrous metals (aluminum alloy, copper alloy).
Features: multi-edge indexable inserts, economical and efficient.
Scenario: mold manufacturing, general machinery batch processing.

How to choose the right Cutting Tool for Lathe?
1. Match the material hardness:
When machining steel parts, wear-resistant coated blades (such as TiAlN) are preferred.
For cutting cast iron, impact-resistant uncoated carbide can be used.
2. Optimize cutting parameters:
Rough machining uses low speed and high feed rate; finishing requires high speed and small cutting depth.
3. Pay attention to the blade geometry:
Positive angle blades are suitable for soft materials, and negative angle blades are suitable for high hardness materials.
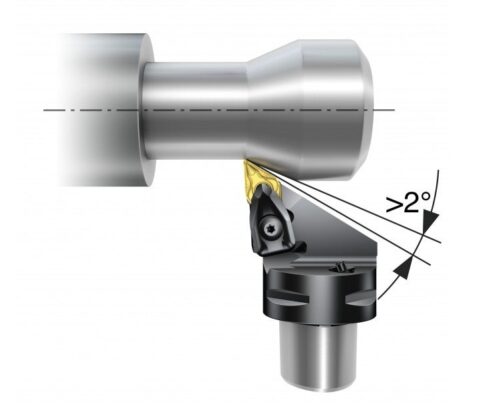
Carbide lathe cutting tools are all-rounders in metal processing. The correct selection can greatly unleash the potential of lathes.
It is recommended to select a suitable blade and toolholder combination based on material properties, processing stage and budget. Whether processing steel or high-temperature alloys, a high-quality Turning Tool can make your production more efficient!