How to choose indexable carbide insert cutting tools?
In the field of modern machining, indexable carbide insert cutting tools have become one of the core tools of industrial production due to their high efficiency, durability and cost-effectiveness.
Whether it is turning, milling or threading, this type of tool can significantly improve efficiency.
But for many processors, how to choose suitable tools and reliable manufacturers is still a challenge.
Today we will analyze the advantages of carbide inserts for you, and focus on how to choose CNC inserts.
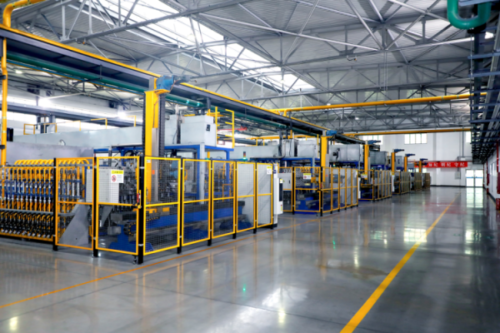
1. Indexable carbide inserts: Why have they become the mainstream in the machining industry?
Indexable carbide inserts are made of tungsten carbide (WC) and cobalt (Co) through powder metallurgy. Their core advantages are:
1. Ultra-high hardness and wear resistance: They can withstand high-speed cutting and high-temperature environments, and their lifespan is 5-10 times that of traditional high-speed steel tools.
2. Indexable design: The polygonal design of the insert allows multiple cutting edges to be flipped, reducing the cost of a single machining operation.
3. Flexible adaptability: By replacing the insert, it can adapt to different materials (such as steel, cast iron, stainless steel) and machining types (rough machining, finishing). This type of tool is particularly suitable for mass production and complex parts machining, which can help users significantly reduce downtime and improve machining accuracy.
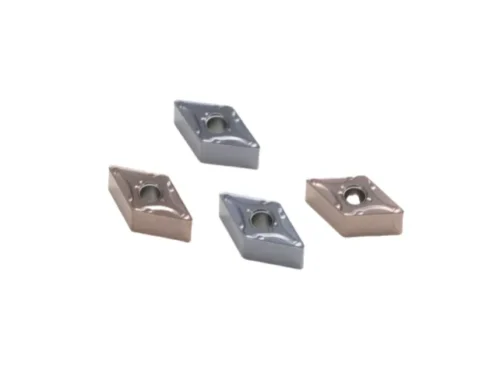
2. How to choose the right carbide insert?
1. Match the processing material: different coatings (such as TiN, TiCN, Al₂O₃) correspond to the cutting performance of different materials.
2. Pay attention to the blade geometry: the front angle, back angle and edge treatment affect the cutting force and surface finish.
3. Give priority to big brands: well-known manufacturers provide technical support and after-sales service to reduce the cost of trial and error.

Indexable carbide insert cutting tools continue to promote the improvement of processing efficiency through technological innovation.
Whether it is general turning, milling or thread cutting, it is crucial to choose a reliable manufacturer and suitable insert model.
Ultimately, high-quality tools can not only reduce costs, but also provide a solid guarantee for product quality.