See how carbide inserts achieve efficient turning, milling and drilling
Whether it is processing 6-inch tungsten steel round bars or dealing with high-hardness alloy materials, tungsten carbide cutting tools and carbide inserts are the core tools to improve efficiency.
As a professional manufacturer, we will analyze the definition and selection skills of cutting tool inserts for you, and recommend high-quality inserts suitable for turning, milling, and drilling to help you easily conquer complex processing challenges!

1. What are cutting tool inserts?
Cutting tool inserts are replaceable modular cutting parts, usually made of superhard materials (such as tungsten carbide), and fixed on the tool bar or tool disc by mechanical clamping. Its core advantages are:
Efficient and economical: only the indexable inserts need to be replaced after wear, without discarding the overall tool, which greatly reduces costs.
Flexible adaptation: The same tool bar can match inserts of different materials to adapt to diverse working conditions.
Performance upgrade: Improve wear resistance and extend service life through coating technology (such as TiAlN, AlCrN).
2. Turning, milling and drilling inserts recommendation and application scenarios
1. Lathe Insert
Recommended model: DNMG160404-PV\43
Features: triangular double-sided 6-edge design, with TiAlN coating, high temperature resistance up to 800°C, suitable for high-speed continuous turning.
Applicable materials: stainless steel, alloy steel, tungsten steel round bar finishing.
Parameter recommendations: linear speed 150-250m/min, feed rate 0.1-0.2mm/rev, surface roughness Ra≤1.6μm.
2. Milling Insert
Recommended model: APKT1604-PDR
Features: negative rake angle design, enhanced tool tip strength, open chip breaker to optimize chip removal, suitable for heavy-duty milling.
Applicable materials: high-hardness cast iron, hardened steel, tungsten steel end milling.
Parameter recommendations: cutting depth 4-6mm, feed per tooth 0.15-0.3mm, suitable for 50-150m/min linear speed.
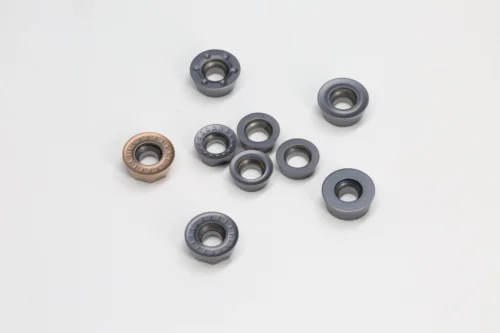
3. U drill insert (Drill Insert)
Recommended model: SPMG060204
Features: double-edged symmetrical structure, internal coolant hole design to reduce cutting temperature, drilling accuracy can reach H7 level.
Applicable materials: deep hole processing of stainless steel, titanium alloy, tungsten steel rod (hole diameter 25-40mm).
Parameter recommendations: feed rate 0.08-0.15mm/rev, linear speed 60-120m/min, with high-pressure coolant.
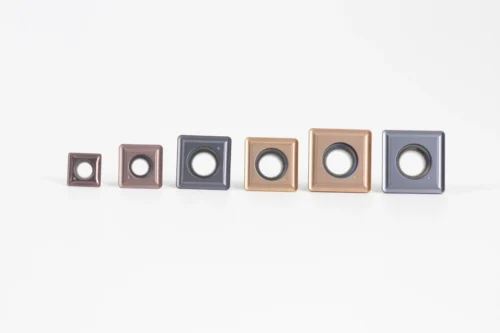
3. Selection logic of tungsten carbide insert
1. Match the groove type according to the processing type:
Continuous cutting: select sharp cutting edge and gentle chip breaker (such as PM groove type) to reduce cutting force.
Intermittent cutting: give priority to strong chip breaker (such as HX groove type) and high-toughness matrix to resist chipping.
2. Select coatings based on material properties:
Stainless steel/high temperature alloys: AlCrN coatings have strong anti-adhesion properties and reduce built-up edge.
Cast iron/tungsten steel: TiCN coatings have excellent wear resistance and are suitable for dry cutting.
3. Determine the number of blades based on cost efficiency:
Mass production: Multi-edge blades (such as the 8-edge SNMG model) reduce unit costs.
High-precision machining: Single-edge precision-ground blades (such as the DNMG model) ensure surface quality.
Whether you need to efficiently turn 6-inch tungsten steel round bars or conquer aerospace alloy parts, our indexable inserts and tungsten carbide tools will be your reliable partners! Let every cutting blade perform to its full potential!